The selection of a suitable high-precision mirror shaft rod requires comprehensive consideration from multiple aspects such as equipment performance, installation structure, and working environment.
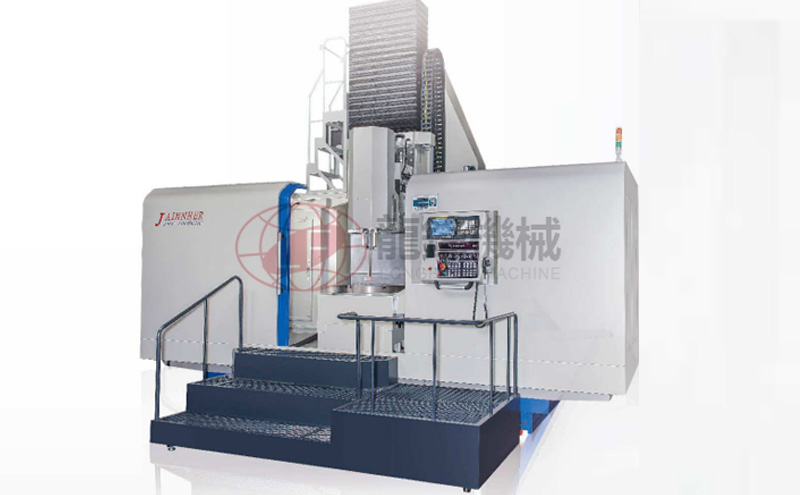
Firstly, confirm the specific requirements of the equipment for the tolerance, roundness, concentricity, and straightness of the shaft and rod dimensions, to ensure a high match with the original design parameters. Select suitable materials according to the usage scenario. Common materials include high carbon chromium bearing steel, stainless steel, and high-strength alloy steel. Different materials correspond to different wear resistance, corrosion resistance, and strength requirements. The operating speed and load capacity of the equipment directly affect the selection of shaft rods, and should be reasonably configured according to the speed level and force analysis. The selection of surface roughness for machining is closely related to the friction characteristics of the mating parts, and fine mirror machining helps reduce wear. The installation structure needs to verify the positioning method at both ends of the shaft rod to avoid operational deviation.
For special application environments, dedicated shaft rods that are resistant to high temperatures, corrosion, or high humidity conditions can be considered. Before use, it is necessary to confirm that the supplied product has undergone strict inspection and meets the internal control quality standards of the enterprise. Reasonable selection helps equipment maintain long-term stable operation and improve overall machining accuracy.