The rust prevention performance of high-precision mirror shaft rods is crucial during long-term use. The anti rust treatment process directly affects the surface quality and service life of the product. The commonly used anti rust treatments currently include physical isolation method, chemical passivation method, vacuum packaging method, and oil film protection method. The physical isolation method forms an effective barrier by coating the surface of the shaft rod with a protective coating, isolating air and moisture from contact. The chemical passivation method involves soaking in a special passivation solution to alter the surface structure of the shaft rod and improve its corrosion resistance.
The oil film protection method uses high-quality anti rust oil evenly coated to form a long-lasting protective layer, while also having good lubrication performance. In some application scenarios, vacuum packaging and nitrogen sealing are used to significantly reduce the risk of oxidation.
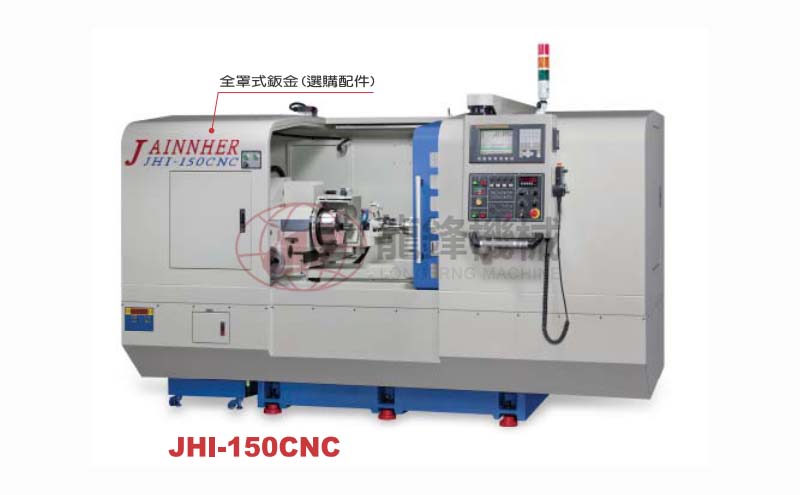
The anti rust process flow is standardized and requires strict degreasing, cleaning, and drying treatment to ensure that the surface of the shaft rod is clean and free of impurities. The humidity of the storage environment in the later stage should be controlled within a suitable range to avoid the adhesion of condensed water. Choosing a reasonable rust prevention process not only effectively protects the surface smoothness of high-precision mirror shaft rods, but also helps to delay material surface oxidation and ensure stable product operation.