高精密鏡面軸棒之所以能在工業(yè)設(shè)備中實(shí)現(xiàn)低摩擦、低噪音與高線性精度的運(yùn)行,關(guān)鍵在于其表面經(jīng)過了多道精細(xì)加工工藝,最終達(dá)到近似鏡面的視覺與物理效果。那么,要打磨出這樣高品質(zhì)的鏡面效果,通常需要幾道工序?
一般而言,一根高精密鏡面軸棒的加工流程大致分為:粗車—精車—熱處理—粗磨—精磨—超精加工—鏡面拋光。其中,真正實(shí)現(xiàn)“鏡面”效果的關(guān)鍵在于最后的超精加工和拋光階段,但前期的每一步也缺一不可。
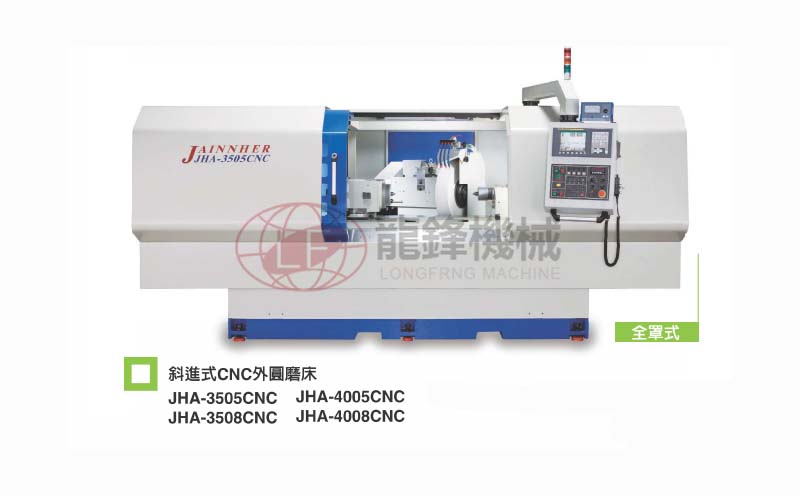
在粗車與精車階段,通過去除材料冗余、形成軸棒初步尺寸;熱處理后提升表面硬度并釋放內(nèi)應(yīng)力;再經(jīng)過粗磨與精磨,逐步將軸棒圓度控制在μm級別。進(jìn)入超精加工階段,采用高精度磨床結(jié)合金剛石砂輪與磨膏,對軸棒表面進(jìn)行細(xì)膩切削,使表面粗糙度降低至Ra0.2μm以內(nèi);經(jīng)由鏡面拋光處理,表面光澤度可達(dá)近似光學(xué)級別,滿足自動(dòng)化設(shè)備與導(dǎo)軌滑動(dòng)系統(tǒng)的應(yīng)用需求。
總體而言,整個(gè)過程通常包含6~8道關(guān)鍵工序,每一步都需嚴(yán)格把控參數(shù)與精度誤差。具備完整加工能力的制造商,往往能實(shí)現(xiàn)從原材料到成品的一體化控制,保障每批鏡面軸棒的一致性與穩(wěn)定性。